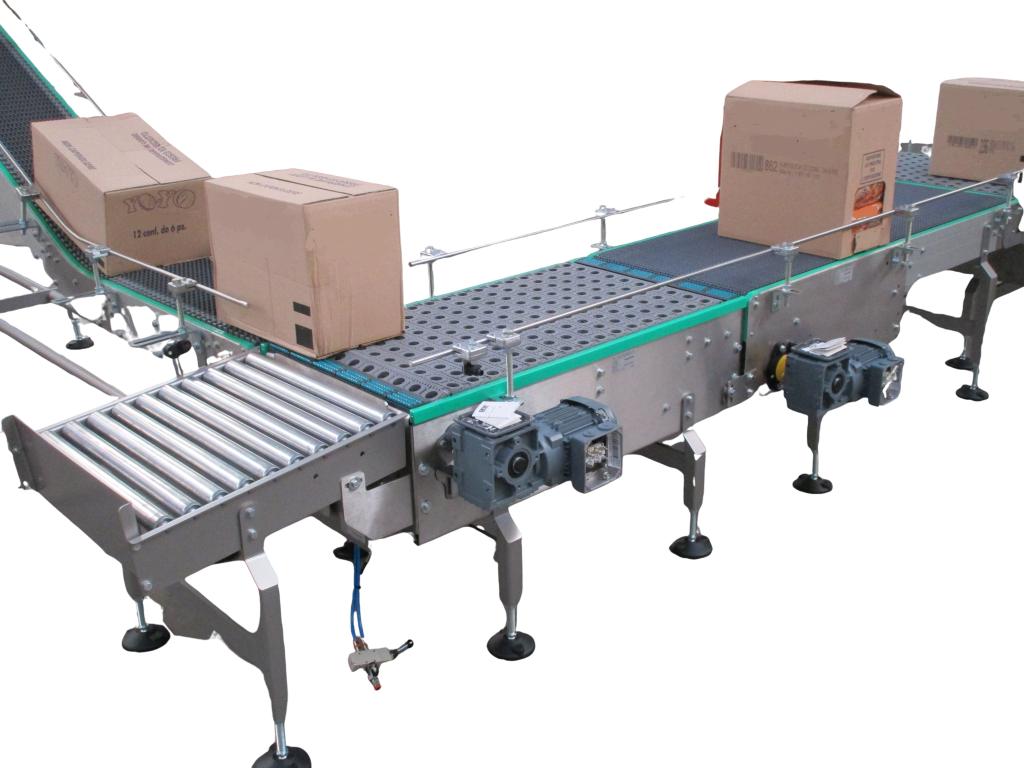
Technology from Material Handling ensures efficient and dependable in the product handling, offering advantages like speed, safety and gentle handling of products.
Sorter systems serve as mechanisms facilitating the diversion of products on a conveyor belt based on specific criteria. Widely adopted in the packaging industry, these systems effectively manage the flow of products—such as cartons, boxes, and trays—to and from packaging lines.
“It’s essential to recognize that not all sorter systems share identical attributes in terms of performance and features”, saids Luca Fontana, commercial director from M.H. Material Handling. “And this article aims to draw a comparison among three distinct sorter systems, each grounded in different technologies: Intralox ARB, Intralox AIM, and Ball Activated Systems.
Intralox ARB and AIM
Intralox ARB relies on rollers integrated into the chain, rotating synchronously with the conveyor belt to facilitate product diversion or sorting. This technology ensures efficient and dependable product handling, offering advantages like: sturdy construction; potential for passive operation without the need for additional pneumatic or electrical drives; reduction in equipment footprint, operational costs, and maintenance, courtesy of its straightforward, modular design.
“Points requiring attention include operator safety and noise, making ARB systems particularly well-suited for end-of-line and palletizer feeding scenarios, where reduced operator presence is common. While logistics is the ideal market, it’s crucial to consider these critical aspects”, continues Luca Fontana. Intralox AIM combines plastic modular belts with pegs embedded in the chain, actuated by pneumatic switches to move products through contact at the chain level.
This technology finds applications in scenarios demanding gentle handling of products, especially in fresh food packaging, where washing with water and detergents is a prerequisite. AIM’s features encompass: suitability for semi-packaged food applications; capability to operate on shallow trays and uneven bottoms, ensuring positive movement without the risk of tripping or damaging products. “Once again, safety and noise considerations are pertinent, but with proper design”, explains Fontana, “AIM stands unrivaled in the meat, fish, ready meals, and dairy industries”.
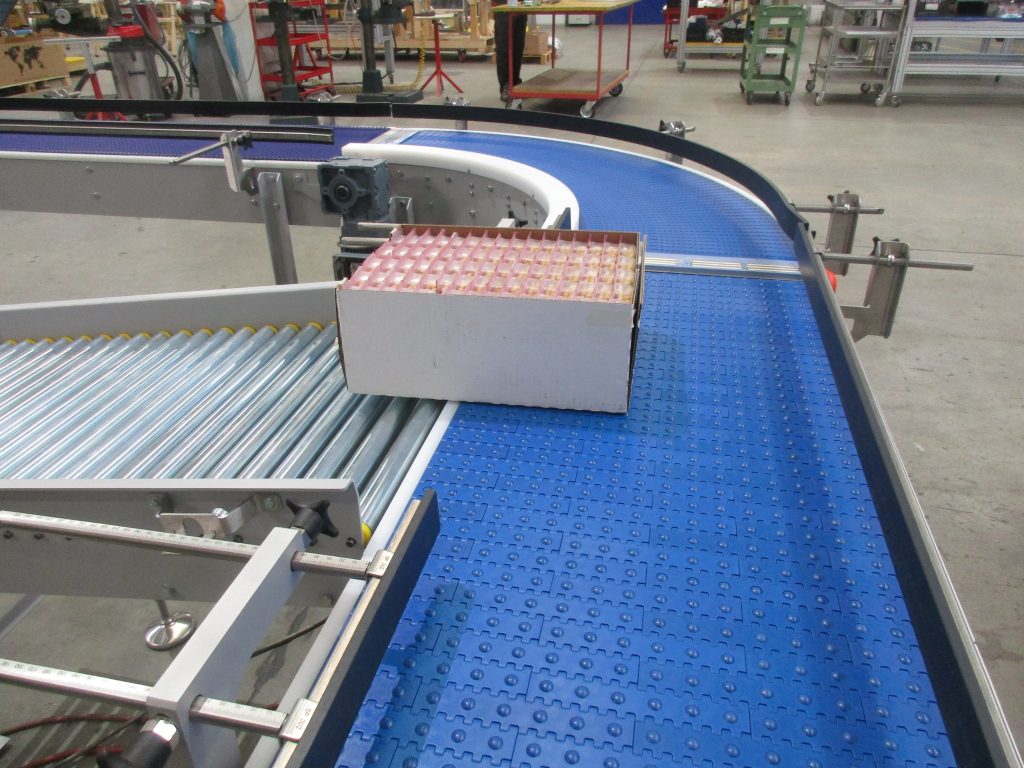
Comparison Magic Sorter/AIM
Magic Sorter employs a modular chain with embedded spheres, driven by an additional belt beneath the main conveyor. Its smaller chain pitch makes it apt for handling smaller and lighter workpieces. Noteworthy strengths of the system include: ability to achieve configurable exchanges in multiple directions within a confined space; enhanced operator protection and reduced noise levels due to the minimized wheelbase.
“However, drawbacks include the need for an additional electric motor for each output and more frequent maintenance checks to prevent ball jams caused by dust or debris released by the products”, concludes Fontana. “While the Magic Sorter exhibits greater versatility, the AIM system remains the preferred choice in washdown areas or when handling products with uneven bottoms. The robustness of ARB systems positions them ideally for applications involving boxes, heavy loads, and overhead installations with limited accessibility”.