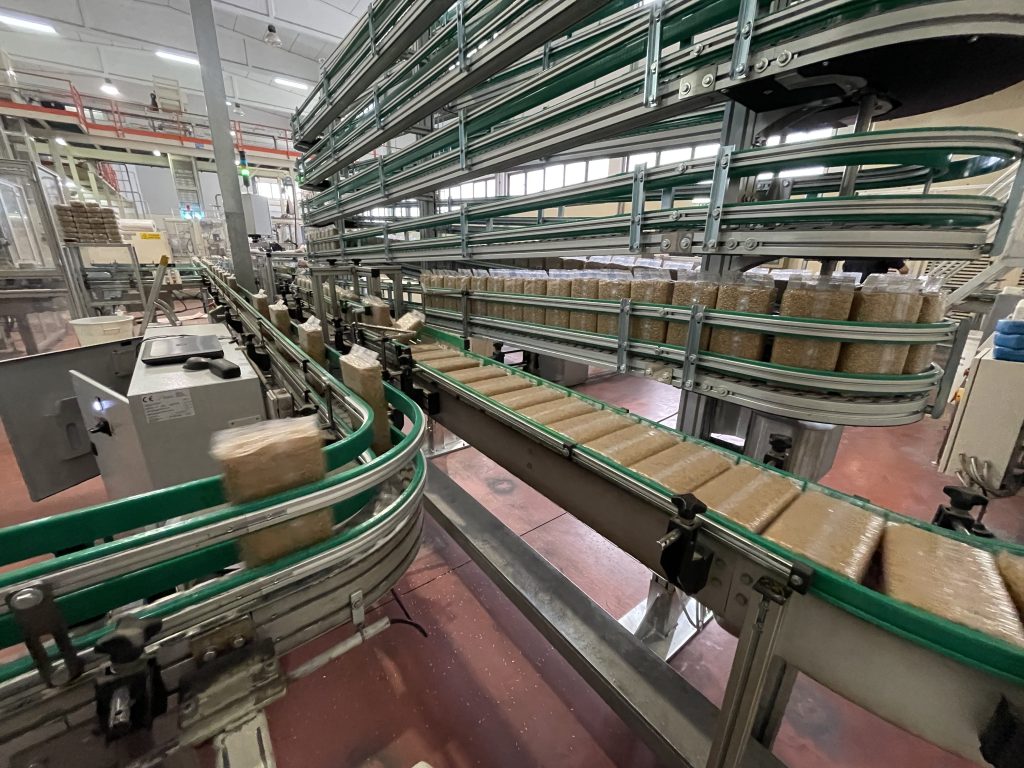
We live years in which the dominant theme, in both mass and industrial communication, is sustainability.
For many, this term immediately and solely recalls that of environmental sustainability, and the impression is that other equally important aspects, not least the economic ones, are being neglected. We can also see this phenomenon in the packaging world, with the right push in the direction of packaging that uses less plastic or is made of innovative and compostable materials.
There is, however, another issue, perhaps taken for granted so far, that is returning to its proper relevance: Production efficiency and waste reduction. Packaging lines are a complex organism, made up of numerous machines in series or in parallel, and, no matter how well constructed and efficient the newer ones may be, the overall efficiency will inevitably decline. Conveyor belts are the circulatory system of this organism and the insertion of a buffer or accumulation system between them is crucial for recovering lost efficiency.
These systems handle operational discrepancies or short stops, keeping production flowing. For example, a machine working intermittently can cause problems when connected to one that requires a constant flow; but while this can often be solved with a few extra metres of parking belt, handling micro-stops requires a conveying system that becomes a real machine.
BAT-Buffer
The BAT-Buffer of M.H. Material Handling is a flexible accumulation system with configurable structure in AISI 304 or anodized aluminium, adaptable to many different products. This spiral device offers up to 150 metres of buffering space with one motor. The machine structure is laid out vertically in spirals with straight sections varying between 2.5 and 6 metres in length and curves with an average radius of 200 mm to minimize side space.
When the downstream packaging line stops, the products are diverted to the spiral track; the load pitch is checked on time to ensure that products do not touch each other. This is very important on long buffer tracks, because otherwise the pressure could damage the products or create overlaps and jams, making the sense of the buffer useless. The system operates with LIFO logic. When the line is restarted, the spiral track reverses its direction, and begins the loading & unloading phase through a merger system that allows to mix what comes from the spiral with the normal production flow.
If the downstream machines have an extra capacity of 10-20%, this layout allows the elimination of losses due to micro-stops at the end of the shift. For typical 3-5-minute buffering capacities, the emptying time is between 15 and 25 minutes when the buffer is completely filled. A further advantage of the BAT-Buffer is the possibility of quickly switching from the loading to the unloading phase, without being forced to fill the buffer. This flexibility of operation has an additional positive aspect on the packaging line, as it allows a continuous production flow without stops. The LIFO logic makes it ideal for baked goods, confectionery, coffee and other products with a long shelf-life as well as products that do not require the cold chain to be maintained.
It will be on display at FachPack 2024, Hall 7A, Stand 757.